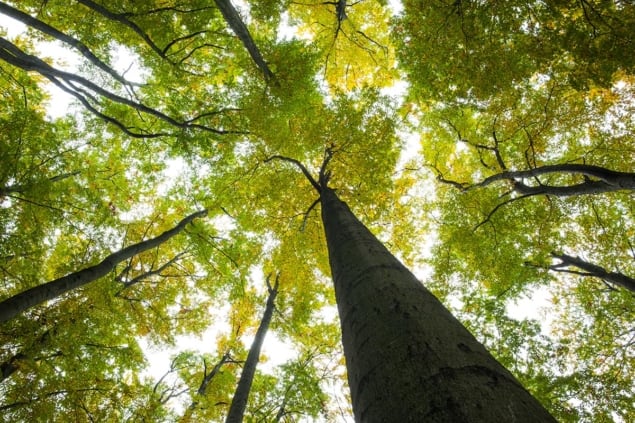
Researchers in the US have developed a new technique that allows wood to be shaped into complex 3D structures. Shaoliang Xiao, Bing Hu and colleagues at the University of Maryland, have shown how useful components can be made by breaking down the molecular structures of wood cell walls, and then moulding the material into desirable shapes. The approach could allow the manufacture of components that are normally made from plastics and metals, but with far lower environmental impacts.
Plastics and metals can be easily processed into lightweight structural components, with widely varying shapes and sizes. This property makes these materials particularly valuable for use in vehicles and buildings, where weight-saving measures are often vital for reducing costs and improving performance. Yet due to the environmental costs of producing metals and plastics, there is now a growing need for more sustainable alternatives.
As a mechanically strong, lightweight, and widely available resource, wood is now being studied as a potential replacement material. Since it is completely renewable, its production can be far more environmentally friendly than metals and plastics, provided it comes from sustainable sources.
Lignin inconvenience
But compared to these materials, wood is also far more difficult to mould into complex shapes. This inconvenience stems from lignin. This is a biopolymer that is a key component of the walls of wood cells, which typically have long, slender shapes running parallel to each other. Although lignin is essential to wood’s mechanical strength, it cannot easily change shape without breaking.
In their study, the researchers showed how the cell walls of wood can be engineered to overcome the challenges posed by lignin’s rigidity. To transport water and nutrients from their roots to their leaves, trees use several different types of wood cell: including “vessels”, which are around 100 micron in diameter, and narrower “fibres”. In the first part of their process, the researchers closed off these transport passages by removing around 55% of the lignin from their cell walls, and then air drying the material to remove any water.
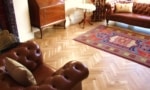
Fungus turns wood piezoelectric, allowing it to power LEDs
Afterwards, the team re-swelled the wood using a “rapid water-shock” process – which selectively re-opened the vessels, while keeping the fibres closed. This technique produced distinctly wrinkled structures in the cell walls – with enough empty space to allow for compression, while also being able to support high levels of strain. This meant that the wood could be easily folded and moulded into different shapes, and then dried to fix its shape.
To demonstrate this, the researchers shaped flat sheets of hardwood into versatile 3D structures: including a honeycomb composite material, which they made by joining specially corrugated sheets. This structure was about six times stronger than the original wood – giving it a similar tensile strength to aluminium alloys, but with a far lower density. Based on their success, the team hopes their technique could soon expand the use of wood as an environmentally sustainable structural material.
The research is described in Science.