Thermal measurements that reveal the complex electrochemical behaviour inside a lithium-ion battery are crucial for designing improved energy-storage devices that last for longer
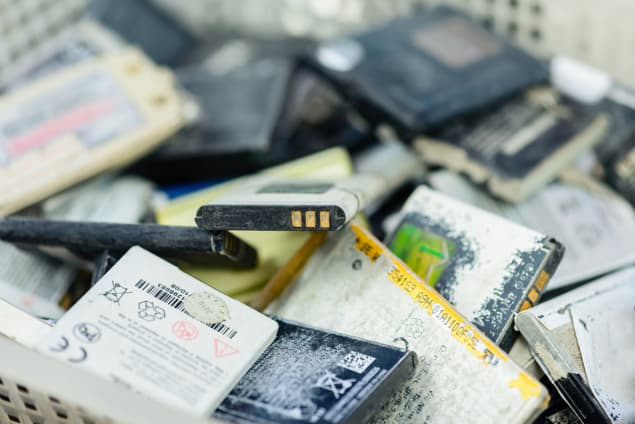
The revolution in mobile technologies has been enabled in large part by advances in rechargeable lithium-ion batteries, allowing more powerful mobile devices with super-sized screens to operate for longer. Unfortunately, however, the battery remains one of the most common points of failure. Thousands of charge-and-discharge cycles take their toll on materials inside the cell, eventually reducing the ability of the battery to store charge and supply power to the device. In the worst cases, thermal runaway in a damaged or degraded lithium-ion battery can become a safety hazard, causing the device to bulge, rupture, and even explode.
To design safer batteries with longer lifetimes, scientists and engineers need a fundamental understanding of the electrochemical processes at play within the cell. That’s why Sascha Nowak and his team in the Analytics and Environment group at the MEET Battery Research Center – part of the University of Münster, Germany – have perfected an array of analytical techniques to probe not just the material properties of the components inside the cell, but also the chemical reactions and mechanisms that cause the battery’s performance to deteriorate over time. “Through comprehensive analysis, our research group gains the in-depth knowledge needed to significantly improve the performance and service life, as well the safety and sustainability, of electrochemical energy-storage devices,” comments Nowak.
In one recent research study, Nowak and his colleagues devised an experimental strategy that exploits a combination of thermal analysis techniques to assess the complex ageing processes that degrade the performance of a lithium-ion battery. “We wanted to establish the reaction mechanisms that are happening inside the battery,” he says. “That could make it possible to design additives or coatings that would slow down these reactions, or even prevent them from taking place.”
Nowak was particularly keen to evaluate the thermal stability of the binder materials that hold together the powdery materials typically used for the electrodes. “The binder is often neglected in studies of the ageing process,” he comments. “Most analyses focus on the electrolyte because it is the most unstable component, or will look at the anodes and cathodes. We wanted to find out how the binder reacts and decomposes at different temperatures to understand the whole battery system.”
To start with, the researchers investigated the decomposition of both anodes and cathodes using a thermogravimetric analyser (TGA) from TA Instruments, which provides precise measurements of the weight loss from the sample over a broad temperature range. They compared the TGA profiles of electrodes in their pristine state with the same components after two charge-discharge cycles and then again after 100 cycles, and in both their charged and discharged states. “We look at the first cycles because there will be some initial decomposition of the electrolyte and some ongoing reactions at the liquid–solid interfaces, and we then measure the profiles after 100 cycles to check whether the system is stable,” explains Nowak. “We also take measurements in both the charged and discharged states, since the presence of lithium inside the anode can influence some of the reactions.”
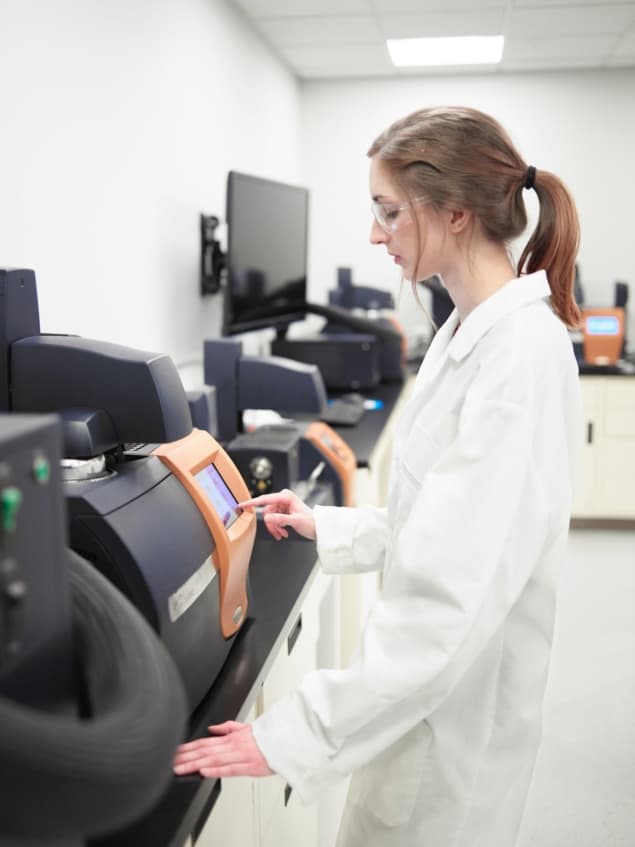
For all the electrodes the TGA analysis revealed significant weight loss at temperatures below 200 °C, which is most likely to be caused by the evaporation of residual electrolyte from the porous electrode structure. The thermal profile of the anodes also revealed two weaker decomposition zones at higher temperatures – one at 200–300 °C and the other at 300–500 °C – which Nowak and his team attribute to the decomposition of two different types of binder. Meanwhile, the TGA profile of cathodes in their charged state exhibits a strong peak between 200–350 °C, which corresponds to the oxygen that is released by a lithium-ion battery cathode during normal operation.
The team then used a differential scanning calorimeter (DSC) from TA Instruments to measure any heat flow within the cathodes – which is a sure sign that chemical reactions are taking place inside the material. No distinct reaction peaks were observed for the pristine sample, or for the newly formed and aged cathodes when in the discharged state. When charged, however, the DSC profile of both cathodes clearly show a strong exothermic reaction at around 270 °C, which is related to the release of oxygen from the cathodes as observed in the TGA analysis.
While TGA and DSC are established techniques for studying the thermal behaviour of battery electrodes, the MEET team exploited another analytical method to investigate the chemical compounds released by the electrodes over a broad temperature range. “We had a pyrolyser that we can heat up to 1000 °C, and attached it to a combined gas chromatograph-mass spectrometer (GC-MS),” explains Nowak. “The chromatograph splits the released compounds into their constituent components, which can then identified by the mass spectrometer.”
The thermal profiles obtained with this technique, called evolved gas analysis mass spectrometry, shows good agreement with the decomposition zones that were observed in the TGA and DSC profiles. Mass spectrometry also confirms that oxygen is released from the cathode at around 270 °C, and also reveals significant evaporation of carbon dioxide from the cathode at temperatures above 250 °C – which could originate from the electrolyte or other organic molecules, including the binder material.
Having identified the decomposition zones from the thermal profiles, Nowak and his team exploited the same combination of pyrolyser and GC-MS to find out which compounds are being released at specific decomposition temperatures. This pyrolysis–GC-MS technique enables a more detailed analysis of the chemical products released from the binders, as well as the separators that are used in batteries to provide a physical barrier between the anode and cathode. “From this study we can conclude that lithiated anodes show intense decomposition behaviour and reactions with electron-rich binder molecules,” comments Nowak. “Meanwhile, charged cathodes are prone to phase changes that can be detected through the release of oxygen.”
While the results from this study offer some important clues about the chemical processes at electrode–electrolyte interfaces, Nowak points out that the main outcome from the work is to provide a starting point for probing the dynamic electrochemical behaviour inside a lithium-ion battery. “This was the first analysis of its kind, and we tried to set the ground rules for what you can do by combining together these different methods,” he comments. “We could show not only the reactions and the weight loss with DSC and TGA, but we could also work out whether the evaporated compounds derived from the electrolyte or from the binder.”
Nowak believes that the same methodology could be used to analyse many other processes inside a lithium-ion battery. “Thermal profiling using a variety of analytical methods turned out to be a valuable tool for the comprehensive analysis of both anodes and cathodes,” he concludes. “From basic characterization right up to detailed investigations of battery ageing, this method set could be used as a tool to unravel the reactions that determine the safety properties of lithium-ion batteries.”
- TA Instruments is part of Waters Corporation, a specialty test and measurement company. More detailed information about the optimal testing solutions for battery materials and components can be found on the Waters/TA Instruments website.