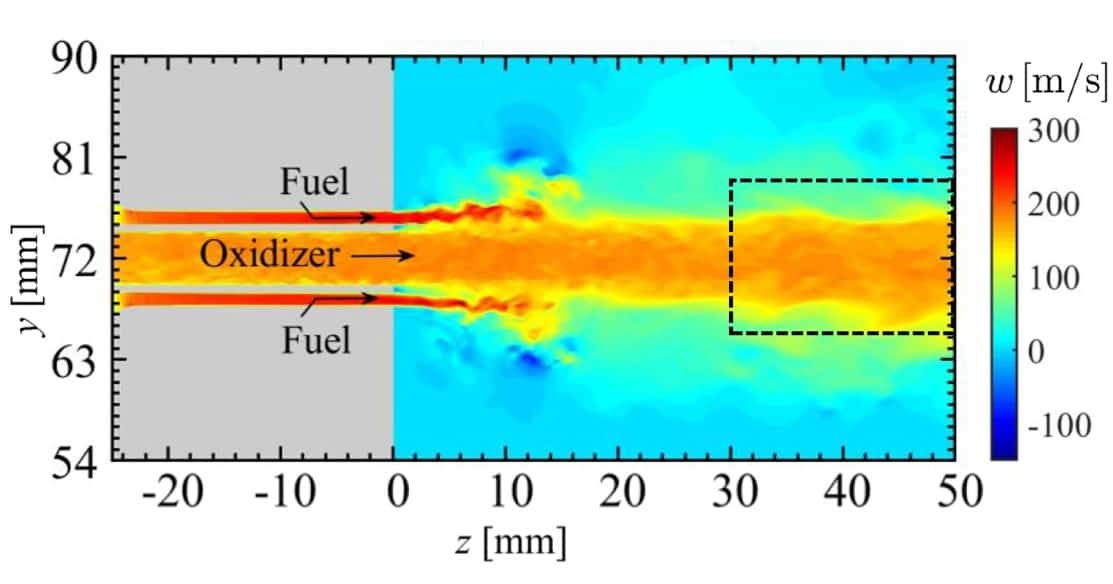
Researchers in Japan have identified a feedback loop that drives damaging combustion oscillations in rocket engines. They found that thermoacoustic power sources created as the oxidizer and fuel flow into the engine’s combustion chamber lead to highly synchronized fluctuations in fuel flow, pressure and heat.
Combustion engines power much of our transport technology and are also used in turbines for power generation. But these engines can develop high-frequency oscillations, which cause structural damage, shortening the life span of combustors and potentially making them unsafe.
“Thermoacoustic combustion oscillations, which are a self-sustaining instability, arise from the strong mutual coupling among hydrodynamics, acoustic waves and heat release rate fluctuations inside a combustor,” Hiroshi Gotoda, a mechanical engineer at Tokyo University of Science, tells Physics World. He notes that they are classified according to combustion chamber pressure fluctuations, depending on the range of dominant frequencies in the chamber, as low- (50 Hz), intermediate- (50–1000 Hz) and high-frequency (above 1000 Hz) oscillations.
Gotoda adds that these combustion oscillations hinder the development of combustors for rocket and aircraft engines, and land-based gas-turbine power plants, because of the unacceptable structural damage they can cause. An in-depth understanding of the causes of these combustion oscillations is needed.
Computational modelling
In their latest research, published in Physics of Fluids, Gotoda and his colleagues used a computational model of a rocket combustor to study combustion events and combustion oscillations, using sophisticated time-series analytical methods, based on based on information theory, symbolic dynamics and complex networks. The aim of the work was to examine the physical mechanisms underlying the formation and sustainment of high-frequency combustion oscillations. In particular, they were interested in the feedback processes between flow velocity fluctuations in the fuel and oxidizer injectors, and pressure and heat release rate fluctuations in the combustor.
Rocket engines use fuel injectors to deliver a fuel, usually hydrogen, and oxygen, the “oxidizer”, to a combustion chamber where ignition and subsequent combustion of the fuel occurs. The researchers discovered a feedback relationship between fluctuations in the flow velocity of the fuel injector and pressure fluctuations in the combustor.
Specifically, they found that pressure fluctuations in the combustor cause flow velocity fluctuations in the fuel injector. This results in the periodic ignition of the unburnt fuel and oxidizer mixture, resulting in significant changes in the ignition location and the heat release rate in the combustor. These heat release rate fluctuations then drive pressure fluctuations in the combustor, which begin to significantly affect the heat release rate fluctuations, by causing flow velocity fluctuations. As this feedback continues, the researchers found that the heat release fluctuations and pressure fluctuations become highly synchronized.
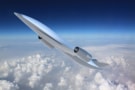
Air-breathing rocket engines: the future of space flight
Gotoda’s study examined a rocket engine with a cylindrical combustor with an off-centre coaxial fuel injector. Fuel flows into the combustor from the outer part of the coaxial injector, while the oxidizer flows from the inner part. The researchers found that thermoacoustic power source clusters developed in the hydrodynamic shear layer region between the oxidizer and fuel. These would form, suddenly collapse and then re-emerge upstream, leading to oscillations in combustion. This repeated formation and collapse was found to play an important role in driving the combustion oscillations.
The researchers believe that their analysis method will lead to a better understanding of the mechanisms behind the formation of combustion oscillations. “The availability of the presented time-series analysis should be shown for various types of combustors,” Gotoda tells Physics World. “The findings obtained in this study shed light on a better understanding of physical mechanism on high-frequency combustion oscillations, and contribute to the academic systemization of nonlinear problems in the field of aerospace engineering and related nonlinear science.”