Perched atop towers hundreds of feet tall, overlooking grassy plains or windy seas, sleek white blades trace slow powerful circles through the air. Can the life cycle of wind turbine blades, lasting about 25 years, be as circular as the elegant arcs they carve in the sky?
This post will follow the wind turbine blade from “cradle-to-grave,” then explore solutions for a more responsible, sustainable life cycle. To learn about the current lifecycle and a more sustainable solution for the rare earth elements in wind turbine generators, read How Are Wind Turbines Made?
Blade materials are special
A wind turbine includes a foundation, a tower, electrical wiring, a nacelle between the blades, and the blades themselves. The raw materials used in the foundation and tower (steel and concrete) and wiring (copper and aluminum) are relatively inexpensive, and the wind industry uses a small fraction of global demand for these materials.
Wind turbine blades are a different story. Blades are made mainly of carbon fiber, fiberglass, and balsa wood and the wind industry drives a significant portion of global demand for these materials: 10% of world demand for fiberglass and 24% for carbon fiber come from wind turbines. While today’s carbon fiber and fiberglass require lots of energy to produce and are hard to recycle, incorporating more bio-materials into their composites and developing new recycling technologies can reduce their footprint. Also, fortunately, the fibers and epoxies needed to make these strong synthetic materials are widely available.
The supply of balsa wood, on the other hand, is highly concentrated in Ecuador and Peru. The high demand for balsa wood in blades for lightweight structural support has linked the wind industry’s demand to increased Amazon rainforest logging and balsa plantation farming. By 2020, demand for balsa wood outstripped supply. Legal and illegal balsa exports have transformed forest landscapes near Indigenous communities with limited consultation or consent of those affected communities.
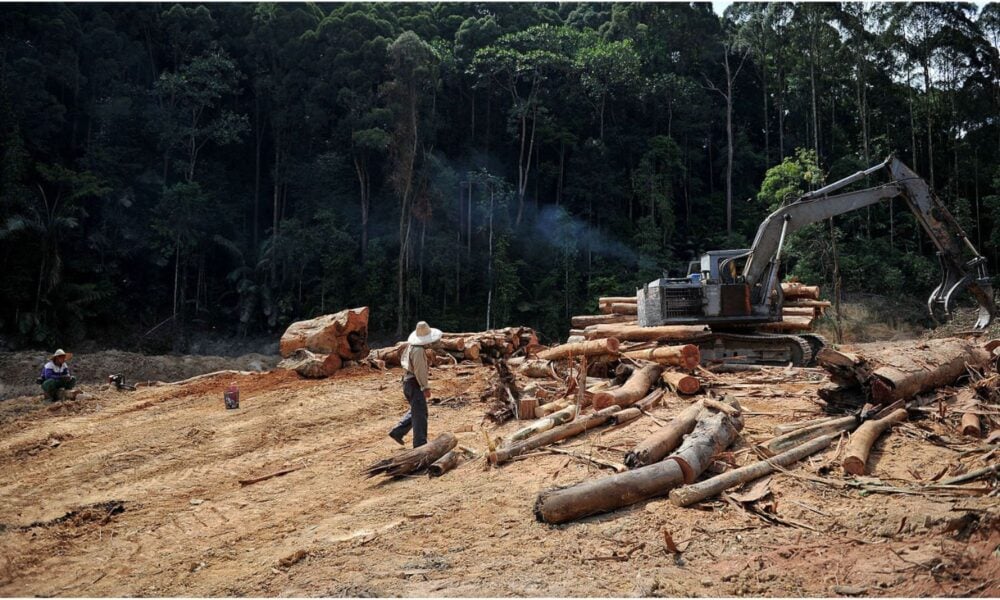
To ensure the wind industry upholds environmental justice and stewards its raw materials, many companies are replacing balsa with other materials. For example, LM Wind Power has minimized balsa in its blades, substituting in synthetic plastic PET and PVC foams. Additionally, INCA Renewtech invented BioBalsa, a durable blade material made of hemp hurd cellulose. The energy research firm Wood Mackenzie estimates that the number of blades using PET as their core material instead of balsa will increase from 20% in 2018 to 55% in 2023.
Can wind turbine blades be recycled?
Yes! The good news is the steel, iron, aluminum, copper, concrete, and electronic components of wind turbine foundations, towers, and wiring can be completely recycled. Recycling the blades is a greater challenge, but an important one to overcome.
In 2021 in the US, 8,000 blades—which each average about 200 feet—were retired. By 2050, the world may be getting 15-18% of its energy from wind, but may also have 43 million metric tons of retired blades to address. Although landfilling of blades does not pose a threat of soil or groundwater contamination and would represent only a tiny fraction of global solid waste streams, the lifecycle of wind turbines would be more circular if there were more options to reuse or recycle the blades.
Composite materials like fiberglass and carbon fiber are tricky to break down, precisely because they are composite, finely blended mixes of different materials which must be separated to be recycled. Those composites make blades hardy and durable, resisting wear and tear for decades.
While today, many retired wind turbine blades end up in landfills, innovative companies have developed repurposing and recycling technologies to help avoid that fate. Veolia, partnering with GE, can shred down fiberglass blades and turn them into cement. Carbon Rivers can transform fiberglass blades into textiles and other synthetic materials, while Global Fiberglass Solutions turns recycled fiberglass into railroad ties and plastic pellets. Vestas and a network of partners have developed the CETEC plan (Circular Economy for Thermosets Epoxy Composites), which in the next three years will be able to separate blade fibers from epoxy and use the epoxy in new blades.
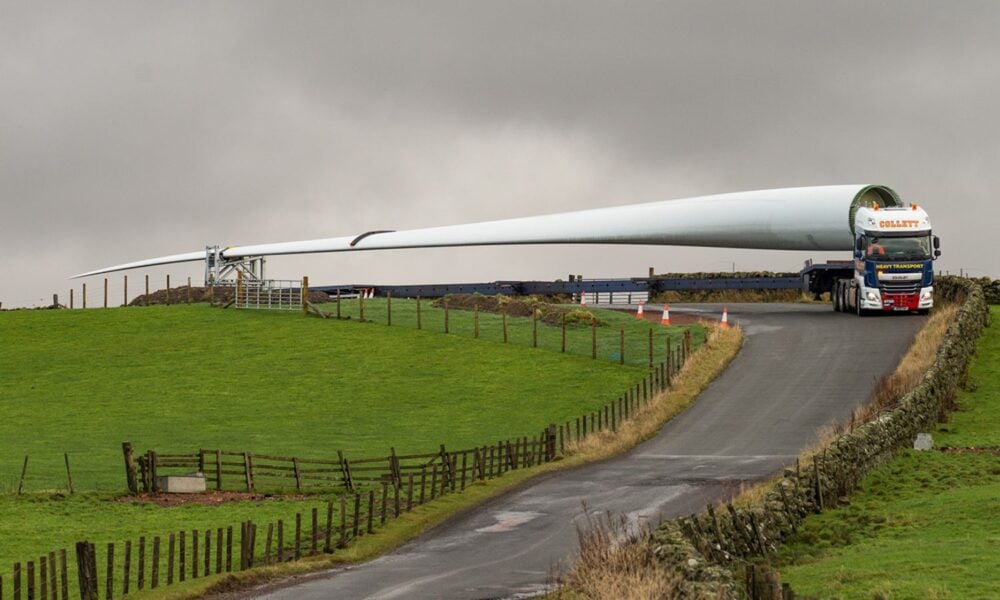
Companies have also started to develop new, more recyclable blade technologies which continue to guarantee strength while facilitating end-of-life processing. For example, Siemens Gamesa installed the first ever recyclable wind turbine blade at an offshore wind farm in Germany in July 2022. It employs a new type of blade epoxy resin. When the blade is immersed in an acidic fluid at high temperatures, the resin dissolves and the components separate, becoming recyclable. The company aims to make all its blades fully recyclable by 2030.
Responsible, circular solutions for wind turbine blades
All wind energy stakeholders, including states, the federal government, companies, suppliers, and consumers, can fuel the responsible, sustainable development of a circular wind energy industry. Some strategies include:
- Ensure an ethical, sustainable supply of balsa wood. Companies can work with their balsa wood suppliers to ensure their materials are sustainably and ethically sourced, and that free, prior, and informed consent of logging- and plantation-adjacent communities is ensured. Governments can support research into, and companies can experiment with, new substitute materials for balsa wood in wind turbines.
- Hold companies accountable for end-of-life management. Extended producer responsibility (EPR) is a proposed concept in which technology companies must plan, execute, and pay for their product’s end-of-life processing through reuse or recycling. The EU has implemented such policies for batteries and solar panels, and governments around the world can follow this model for wind turbine blades. They can also reward companies that recycle their blades through incentives.
- Accelerate the use of recycled materials in new blades. To create a circular economy for recycled blades, there must be a market. Blade manufacturers must establish contracts with today’s nascent blade recyclers to speed up the transition to using recycled materials in new blades.
- Increase recyclable blade research and development. States and the federal government can provide competitive grants, research funding, and incentives to labs and companies innovating new recyclable blade chemistries.
When we think about wind turbines, we visualize big circles high in the sky. The wind turbine blade life cycle can be just as circular. Governments, industry, and consumer commitments are moving us towards even more responsible, sustainable blade supply chains and end-of-life management.
How are wind turbines made? What happens when wind turbines reach the end of their service lifetimes? What will it take to ensure those colossal, majestic blades don’t end up in landfills? Where do their raw materials come from, and when they retire, can we process those materials into other useful products or recycled blades? How can we move towards a sustainable, responsible wind energy supply chain, and ensure all materials come “full circle”? Click the links below for answers:
Just and Sustainable Solutions for the Mining and Recycling of Rare Earth Elements in Wind Turbines
Now that you’ve learned about wind power, are you interested in the life cycle of solar panels? Read on:
Mining Raw Materials for Solar Panels: Problems and Solutions